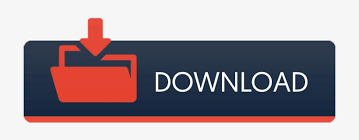
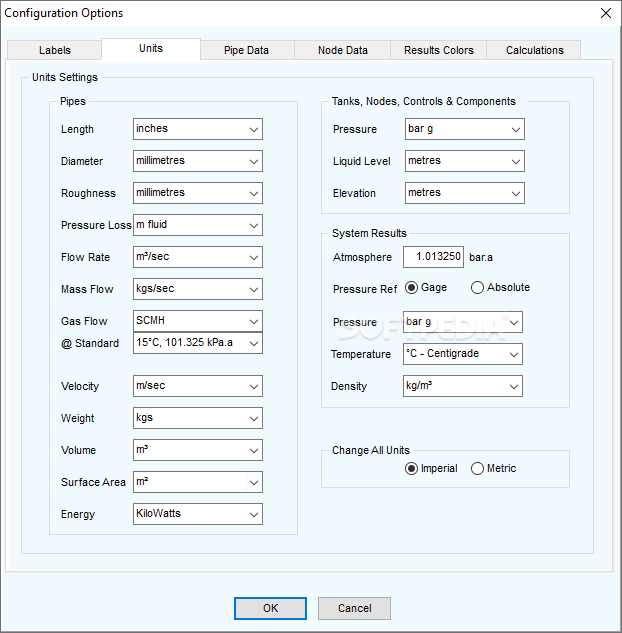
The Pipe Flow Module allows the mapping of data from edges, to surfaces, and to volumes, and vice versa. These systems can easily be coupled to other systems that cannot be described using the approximative methods in the Pipe Flow Module, but require a full description of the system's physics in 2D or 3D. The physics in the Pipe Flow Module describe the conservation of momentum, energy, and mass in the fluids inside a pipe or channel system.

Coupling Pipe Flow to Other Physics and Applications This app simulates the balance between temperature requirements and pressure drop (running costs) together with construction and material costs (fixed costs) for different floor materials and and dimensions. It delivers more uniform heating to a room than convector fans or wall radiators would. Underfloor heating and cooling is a form of central heating and cooling which achieves indoor climate control for thermal comfort using conduction, radiation and convection. COMSOL Multiphysics ® also allows you to bring in data to describe a certain material property or process parameter, as well as subroutines written in MATLAB ®. As with any physics interface in the COMSOL Product Suite, you can freely manipulate the underlying equations, add your own source or sink terms, and express physical property as functions of any model variable.

The Pipe Flow Module also considers the effects of bends, contractions, expansions, T-junctions, and valves that are computed through an extensive library of industry standard loss coefficients, while pumps are also available as flow-inducing devices.
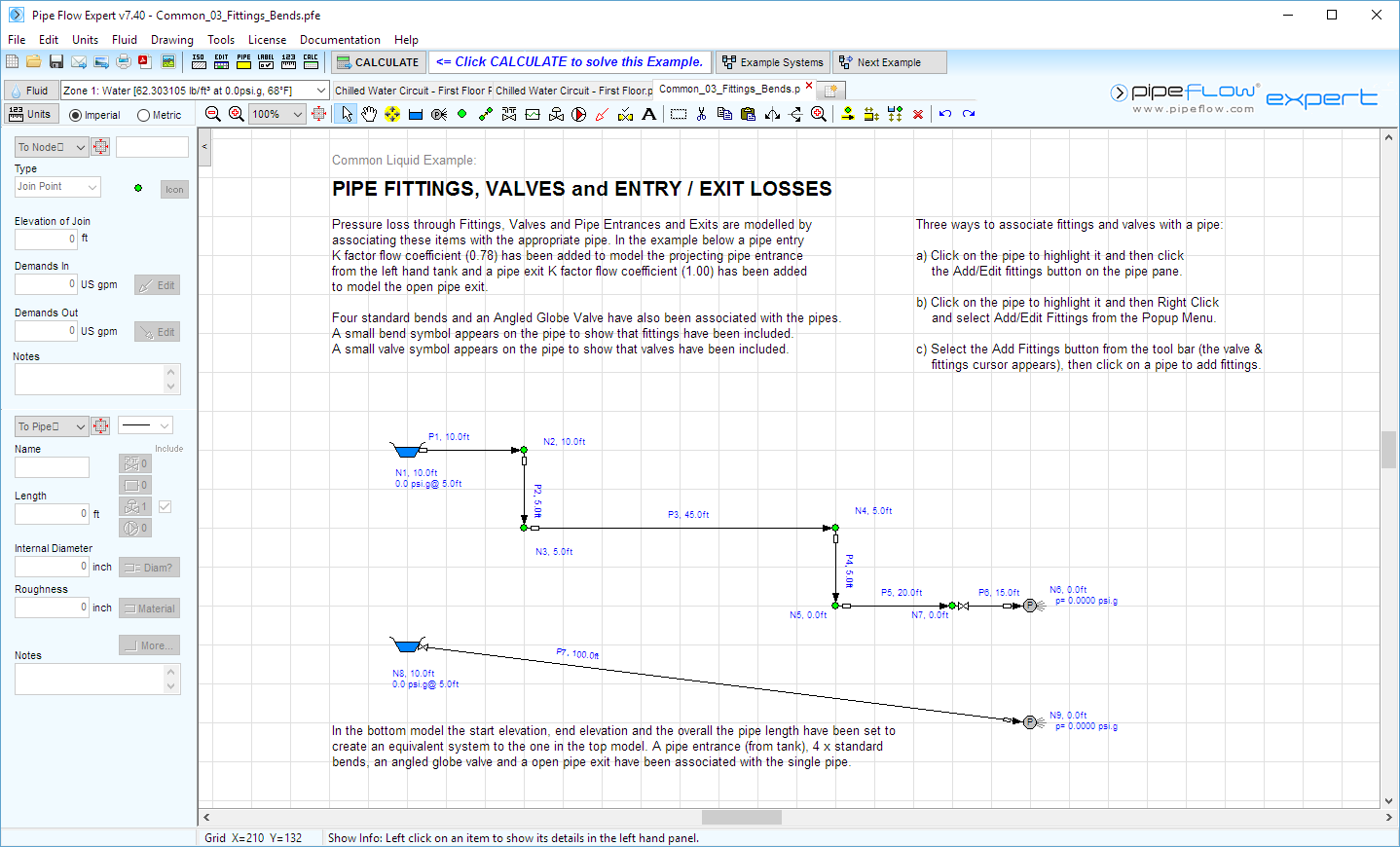
These can be varied according to their position in the network, or directly related to the variables you are modeling.įriction is not the only contribution to pressure loss in pipe networks. Built-in expressions for Darcy friction factors cover the entire flow regime including laminar and turbulent flow, Newtonian and non-Newtonian fluids, different cross-sectional shapes or geometries, and a wide range of relative surface roughness values. This means that the modeled variables are averaged in the pipe's cross sections and vary only along the length of the pipe. With this assumption it uses edge elements, solving for the tangential cross-section averaged velocity along the edges, to avoid meshing the cross section of the pipe with a full 3D mesh. The Pipe Flow Module is suitable for modeling incompressible flow in pipes and channels whose lengths are large enough that flow can be considered fully developed. Ideal for Modeling Incompressible Fluid Flow Regimes Pipe flow simulations provide the velocity, pressure, material concentrations, and temperature distributions along pipes and channels, while it can also simulate acoustic wave propagation and the water hammer effect. This allows for the conservation of computational resources in your overall modeling of processes that consist of piping networks, while still allowing you to consider a full description of your process variables within these networks. It can be easily integrated with any of the other modules in the COMSOL ® Product Suite for modeling the effects piping has on larger entities, such as cooling pipes in engine blocks or feeding and product channels connected to vessels. The Pipe Flow Module is used for simulations of fluid flow, heat and mass transfer, hydraulic transients, and acoustics in pipe and channel networks. Consider All Process Variables with Reduced Computational Resources
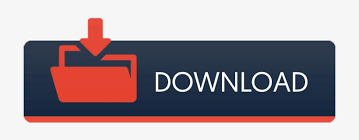